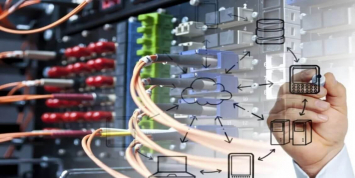
- Главная
- >
- Роботы с искусственным интеллектом
- >
- ИИ сокращает время необходимое для точного прогнозирования срока службы батарей
ИИ сокращает время необходимое для точного прогнозирования срока службы батарей
Машинное обучение может сократить время тестирования, необходимое для новых батарей и электроники , на годы. За последние несколько десятилетий аккумуляторы стали намного эффективнее, но определение срока их службы все еще чрезвычайно сложно и отнимает много времени. Чтобы лучше предсказать, как долго будут работать батареи для нацеливания на соответствующие устройства,Toyota Research Institute (TRI) решило решить эту проблему.
Сложности проверки
Несмотря на большой прогресс в данной технологии, это усложняет их проверку. Когда батареи имеют короткую жизнь, легко сделать тщательное испытание, но по мере увеличения срока жизни аккумуляторов, все сложнее и сложнее проводить испытания для определения их срока жизни.
Чтобы ускорить процесс, команда MIT / Toyota использовала ИИ как способ точного прогнозирования срока службы батареи с 95% точностью, обучив его нескольким сотням миллионов вариантов развития событий и учитываяперепады напряжения и другие факторы. По словам команды, можно определить, имеет ли аккумулятор длительный или короткий срок службы, взглянув на пять циклов зарядки / разрядки.
Новый метод
Новый метод машинного обучения и его набор данных могут быть использованы для ускорения разработки новых аккумуляторов при одновременном снижении затрат как на исследования, так и на производство, особенно на их сборку и изготовление. Это может сократить время, необходимое для проверки новых батарей.
Таким образом, можно было бы определить, достаточно ли в них осталось ресурса для повторного использования. В дополнение к этому метод прогнозирования может помочь оптимизировать аккумулятор, сократив время зарядки до 10 минут, а время оптимизации батареи может быть уменьшено в 10 раз.
«Несмотря на все время и деньги, которые тратятся на разработку аккумуляторов, прогресс все еще измеряется десятилетиями», - говорит Патрик Херринг из Toyota. «В этой работе мы сокращаем один из самых трудоемких этапов - тестирование аккумулятора».
Похожие статьи:
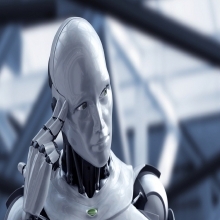
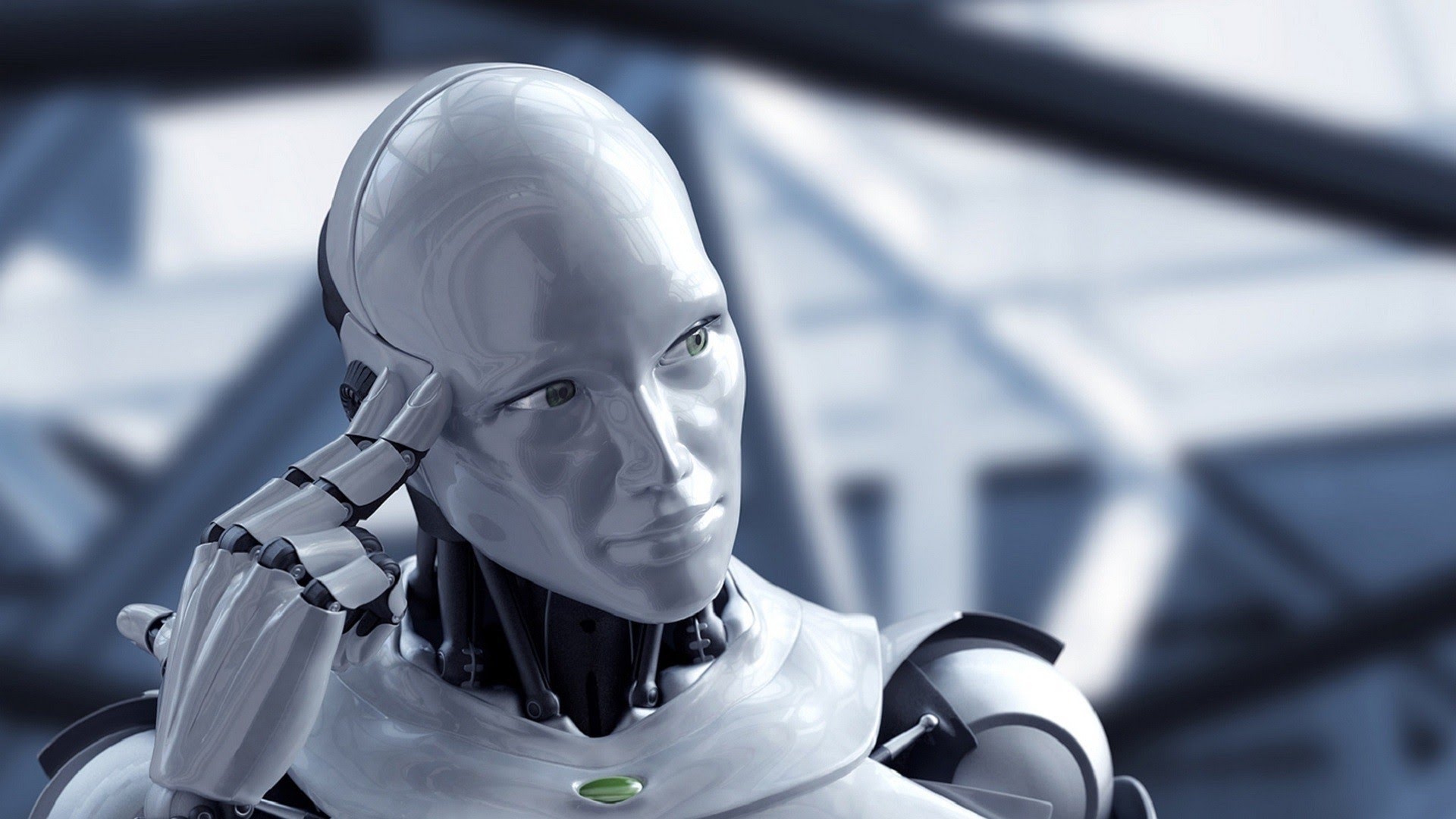
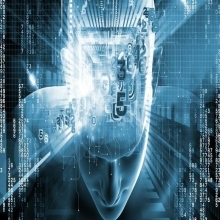
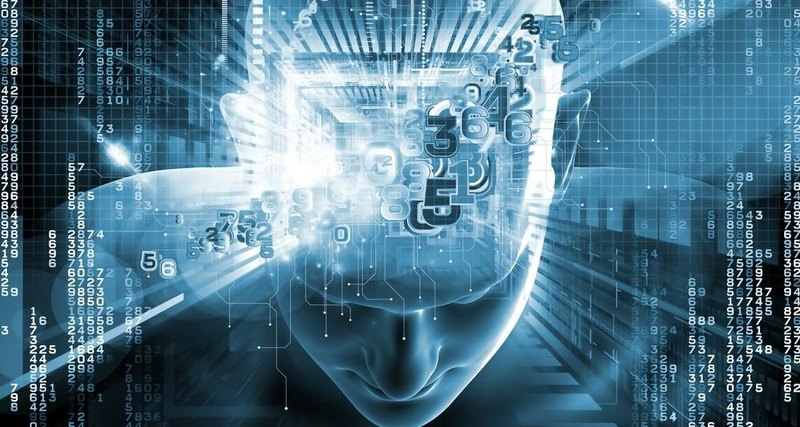
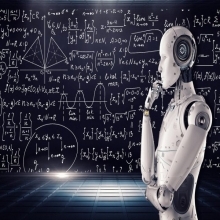
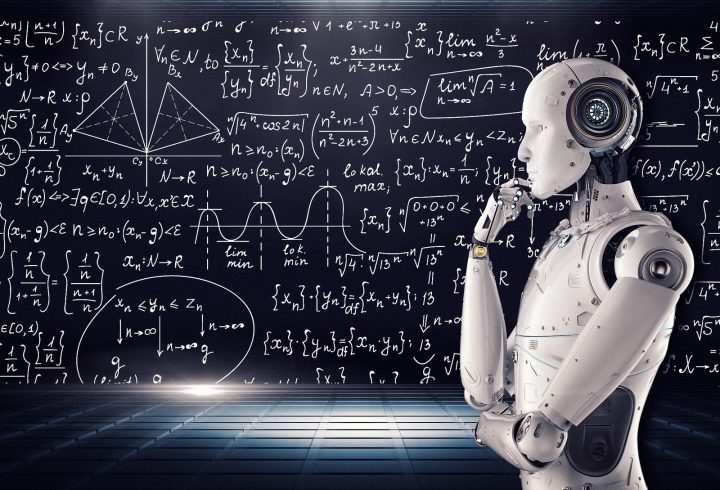
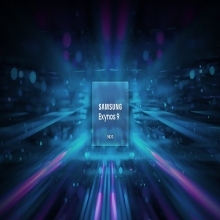
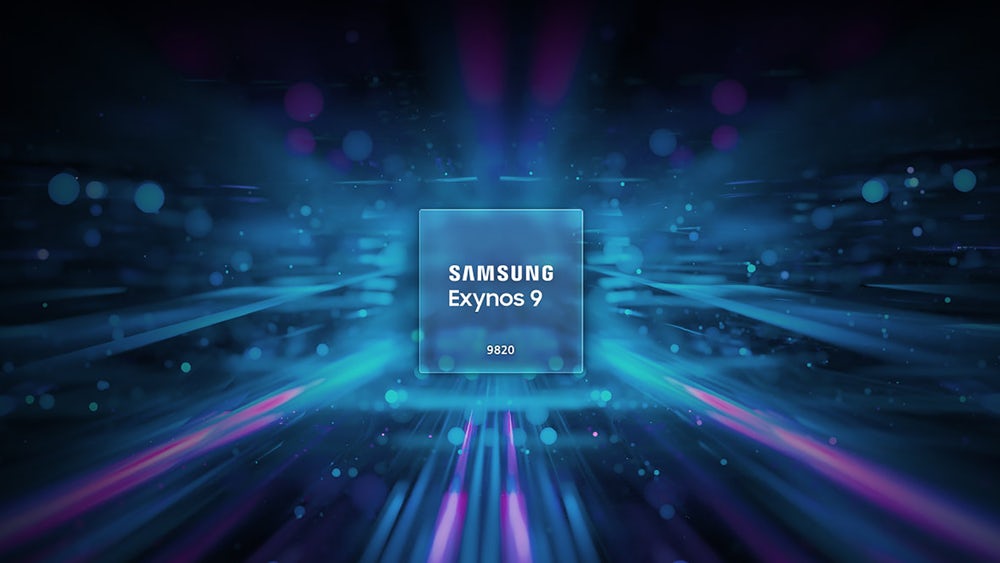
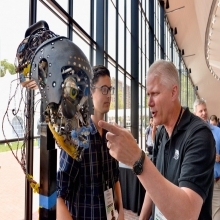
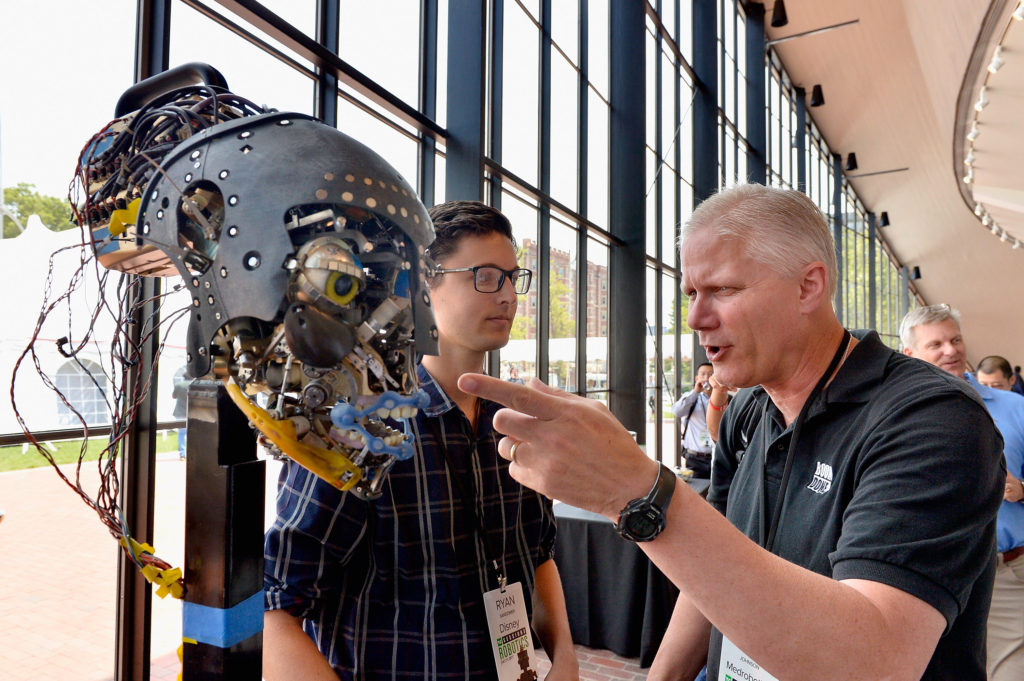
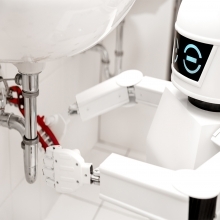
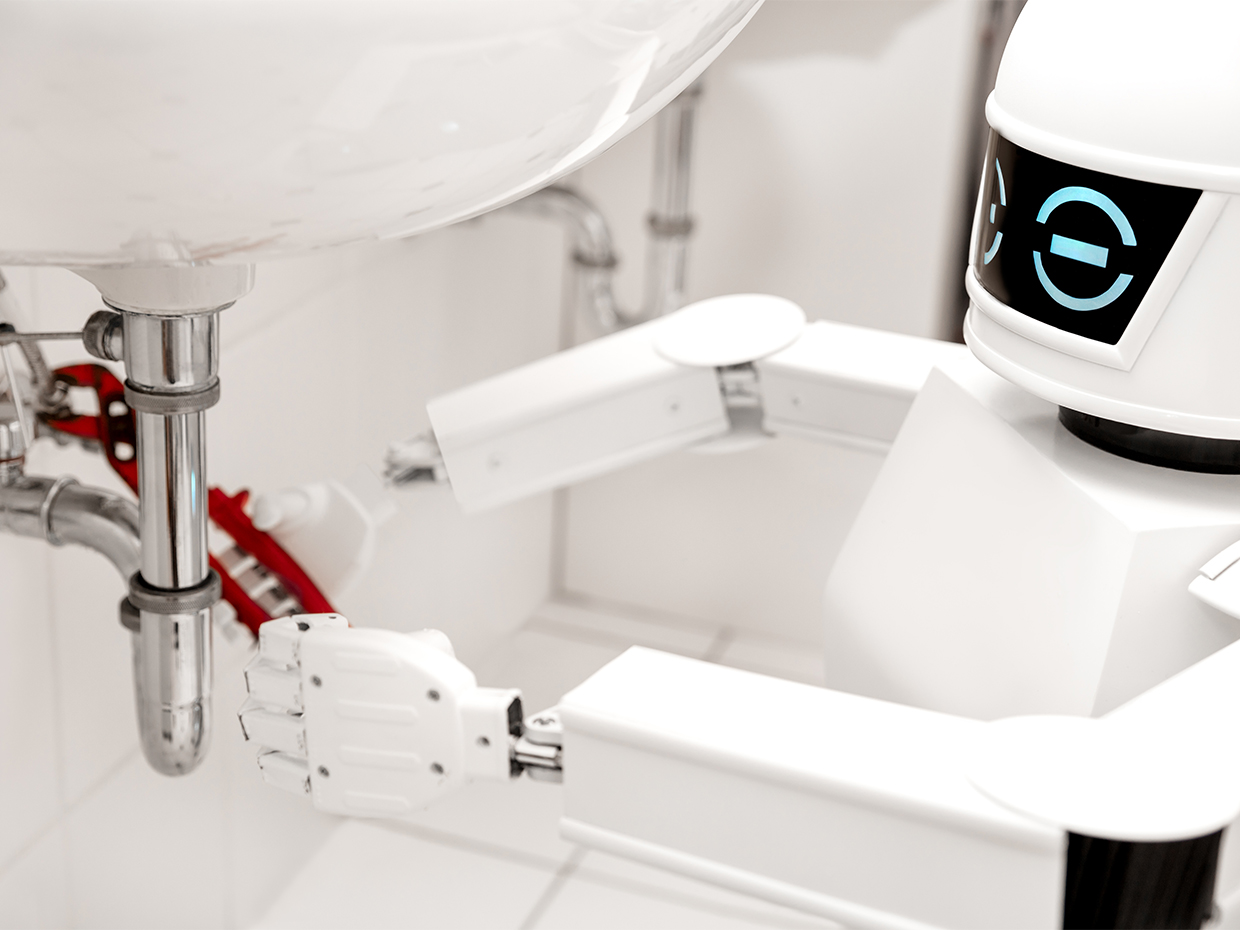