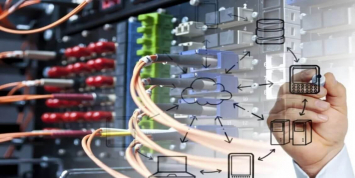
- Главная
- >
- Новости
- >
- Для изготовления более прочного и экологичного бетона исследователи используют 3D-принтер
Для изготовления более прочного и экологичного бетона исследователи используют 3D-принтер
Исследователи из Калифорнийского университета в Беркли разработали новую технологию армирования бетона с помощью полимерной решетки - шаг вперед, который может соперничать с другими новшествами на основе полимеров и улучшить пластичность бетона при одновременном снижении выбросов углерода во время производства материала.
О новом исследовании
Исследователи из Беркли использовали 3D-принтер для создания балок, укрепленных полимерной решеткой. Специальная камера показывает, что при испытании на изгиб балки обладают большой гибкостью и прочностью. Этот метод, о котором сообщалось в номере журнала Materials and Design, может повысить привлекательность бетона, одного из наиболее широко используемых искусственных строительных материалов. Он дешевый, массивный и прочный, способный выдерживать очень большие нагрузки. Но бетон, как известно, слаб при растяжении или изгибе.
Он хрупкий и при разрыве начинает трескаться. Без армирования бетонная конструкция может внезапно разрушиться. С середины 19 века инженеры стали использовать при производстве бетонных балок железную арматуру. Но из-за этого у материала появился ряд недостатков: он тяжелый, дорогой в производстве, трудоемкий в установке и со временем портится. Сегодня растет сообщество инженеров, изучающих возможность армирования бетона полимерами, которые привлекают исследователей, поскольку они легкие, не подвержены коррозии и из-за большого количества перерабатываемых материалов могут быть дешевыми в производстве.
«Когда материал хрупкий, он может выдерживать определенную пиковую нагрузку, а затем выходит из строя», - сказала соавтор исследования Клаудиа Остертаг. «В данном случае мы не наблюдали сбоя. Он становился все сильнее и сильнее. Для нас, интересующихся бетоном, это удивительно.
Нам удалось сделать его очень пластичным». С 1960-х годов инженеры армировали бетон полимерными волокнами. Концепция не нова. Волокна использовались для укрепления раствора с древних времен - вспомните о соломе, добавляемой в сырцовые кирпичи. Но это не идеальное решение. Волокна замешиваются в бетон перед его заливкой и редко распределяются равномерно. Это означает, что в одной части структуры может быть высокая концентрация волокон, а в другой их почти нет, из-за чего могут образоваться трещины. Преимущество решетчатой арматуры состоит в том, что она останавливает процесс появления трещин до того, как они станут слишком большими.
Проблемы, возникавшие ранее и пути их решения
Предыдущие эксперименты с полимерными решетками были вдохновлены природой, в том числе внутренней частью раковин морских ушек и сотовой формой ульев. Но это армирование было двумерным, что ограничивало их способность выдерживать сложные бетонные конструкции.
Чтобы создать трехмерную конструкцию, которая могла бы выдерживать большие нагрузки со всех сторон - что инженеры называют изотропными, - исследователи из Беркли использовали октетную ферму для создания решетчатой структуры. Популяризованная архитектором Бакминстером Фуллером в 1950-х годах, октето-ферма известна своей прочностью и невероятной легкостью.
В начале 1900-х годов Александр Грэм Белл использовал его для изготовления воздушных змеев. Проект основан на предыдущих исследованиях, проведенных Ostertag, чья лаборатория впервые предложила идею использования структуры октетной решетки с бетоном со сверхвысокими характеристиками. Автор нового исследования - Хайден Тейлор, доцент кафедры машиностроения, и Брайан Салазар, доктор философии.
Тестирование прототипов
Команда протестировала два разных полимера: полимолочную кислоту (PLA), которую легко напечатать на 3D-принтере, но более хрупкую, чем другие полимеры, и акрилонитрилбутадиенстирол (ABS), который прочнее, чем PLA, и используется во всем, от деталей Lego и мотоциклетных шлемов до каноэ и автомобильных бамперов. Переход с PLA на ABS не оказал существенного влияния во время испытаний на сжатие: все образцы железобетона с решетчатой арматурой имеют высокие значения плотности и устойчивы к деформации, что означает, что они были способны поглощать много энергии.
Инженеры также поэкспериментировали с количеством решетчатой арматуры, используемой в бетоне. Один образец был тоньше, где полимер составлял 19,2% от объема образца. Другой составил 33,7%. Увеличение количества полимера в образцах несколько снизило их прочность на сжатие, но увеличило их пиковые нагрузки. Важно отметить, что количество полимера существенно не изменило общие механические свойства конструкции. Образцы с меньшим количеством полимера были такими же прочными, как и образцы с большим их содержанием.
Но есть случаи, когда большее количество полимера может иметь значительные преимущества. На производство цемента, основного ингредиента бетона, приходится 8% мировых выбросов двуокиси углерода. В большинстве бетонных конструкций арматурный материал составляет менее 5%. Таким образом, увеличение количества полимера - и уменьшение количества бетона - может сократить общие выбросы углерода при создании конструкции. «Реакция, при которой образуется цемент, по своей сути производит CO2», - сказал Тейлор.
«Напротив, существует возможный путь к созданию полимеров, которые являются чистыми углеродно-нейтральными или даже потенциально углеродно-отрицательными, за счет использования биополимеров, вторичной переработки и возобновляемых источников энергии». Следующим шагом, по словам Салазара, будет определение того, будут ли различные формы использования бетона лучше обслуживаться решетками других форм.
В будущем инженеры могут определить наилучшую геометрию армирования для конкретного проекта с помощью программного обеспечения для оптимизации исследований. «Забегая вперед, вопрос останется только один - как выбрать лучшую решетчатую структуру для конкретного приложения», - сказал Салазар. «Могут быть найдены еще более оптимальные геометрические формы».
Похожие статьи:
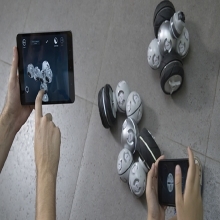
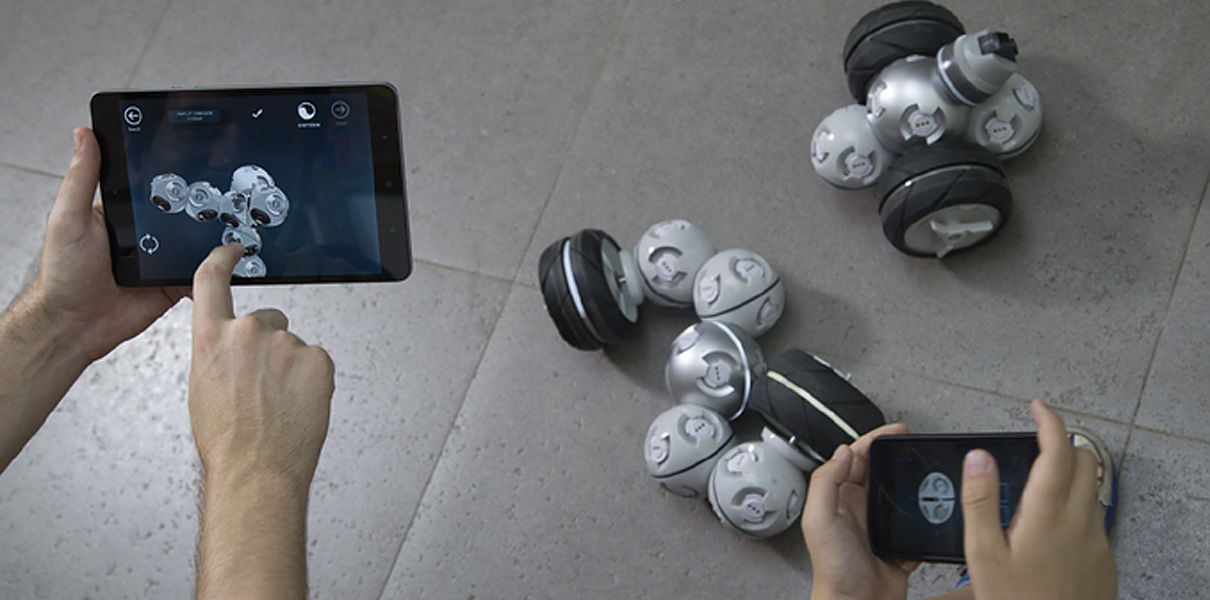
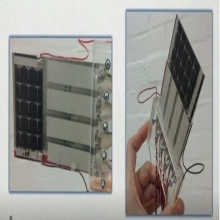
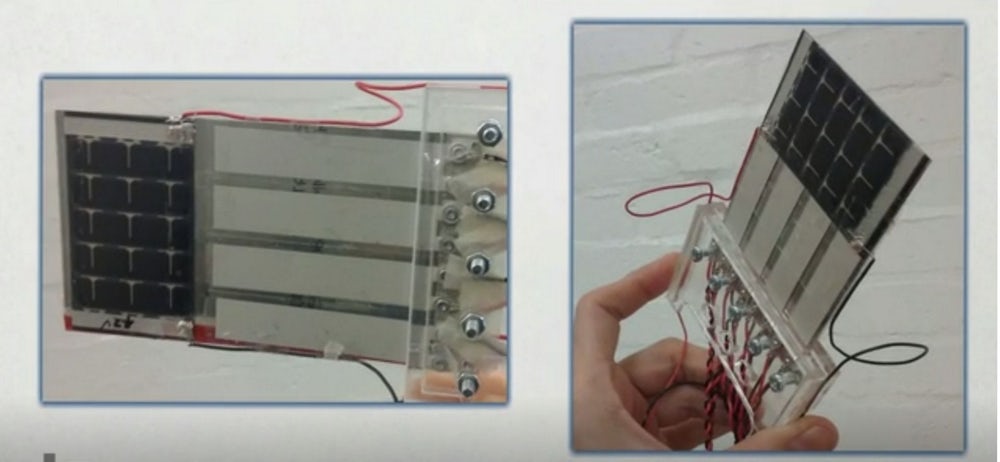

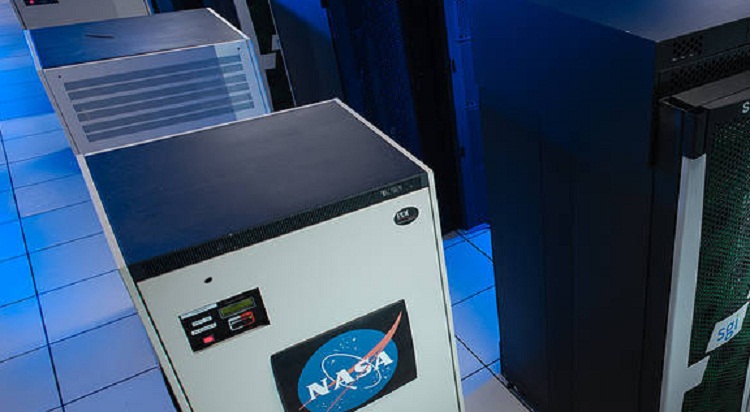
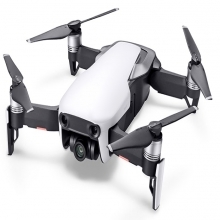
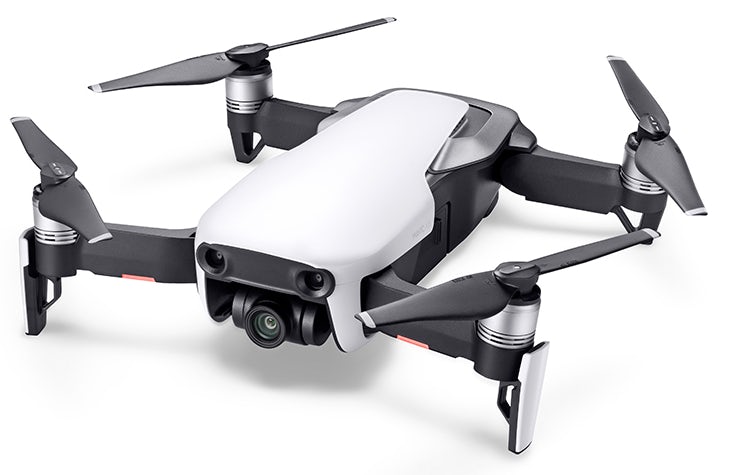
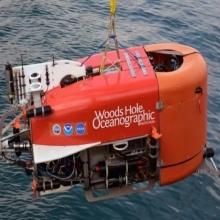
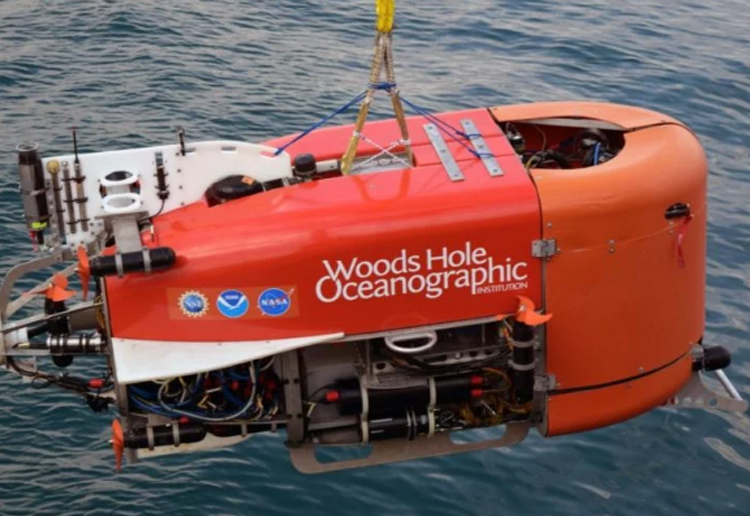
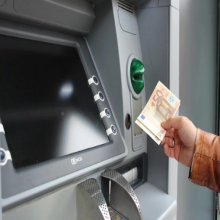
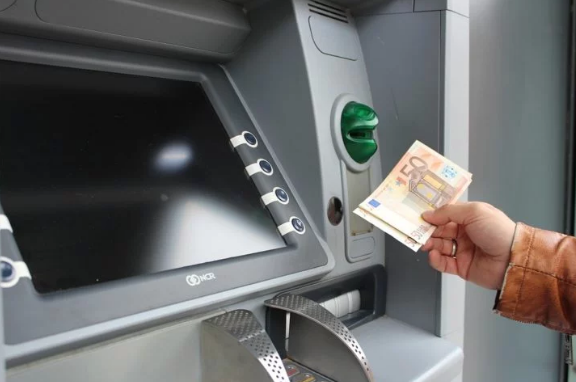